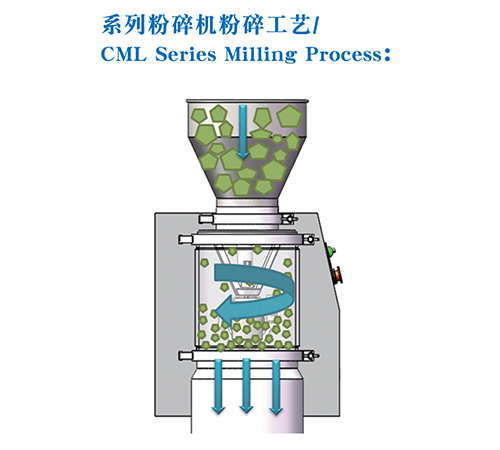
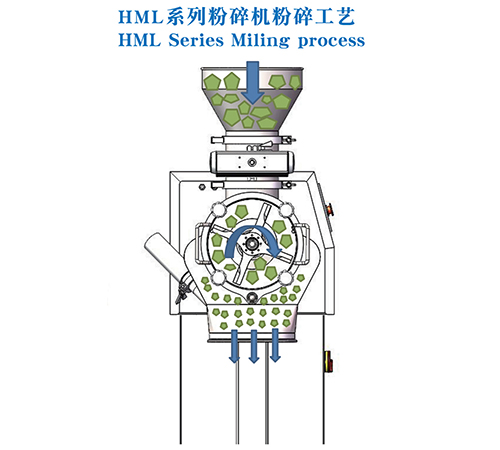
കോൺ മില്ലിങ്
ഫാർമസ്യൂട്ടിക്കൽ ചേരുവകളുടെ വലിപ്പം ഒരു ഏകീകൃത രീതിയിൽ കുറയ്ക്കുന്നതിന് പരമ്പരാഗതമായി കോൺ മില്ലുകൾ, അല്ലെങ്കിൽ കോണാകൃതിയിലുള്ള സ്ക്രീൻ മില്ലുകൾ ഉപയോഗിക്കുന്നു. എന്നിരുന്നാലും, അവ മിക്സിംഗ്, അരിച്ചെടുക്കൽ, ചിതറിക്കൽ എന്നിവയ്ക്കും ഉപയോഗിക്കാം. വലിയ ഫാർമസ്യൂട്ടിക്കൽ പ്രോസസ്സിംഗ് പ്രവർത്തനങ്ങൾക്ക് ഉപയോഗിക്കുന്ന ടേബിൾടോപ്പ് ലബോറട്ടറി ഉപകരണങ്ങൾ മുതൽ പൂർണ്ണ തോതിലുള്ള ഉയർന്ന ശേഷിയുള്ള മെഷീനുകൾ ഉൾപ്പെടെ വിവിധ വലുപ്പങ്ങളിൽ അവ വരുന്നു.
കോൺ മില്ലുകളുടെ ഉപയോഗങ്ങൾ വ്യത്യസ്തമാണെങ്കിലും, ഫാർമസ്യൂട്ടിക്കൽസിൽ അവ ഉപയോഗിക്കുന്നതിനുള്ള പ്രവണത ഉൽപ്പാദന സമയത്ത് ഉണക്കിയ വസ്തുക്കളെ നീക്കം ചെയ്യുന്നത് ഉൾപ്പെടുന്നു; ഉണങ്ങുന്നതിന് മുമ്പ് നനഞ്ഞ ഗ്രാനേറ്റഡ് കണങ്ങളുടെ വലുപ്പം; ഉണങ്ങിയ ഗ്രാനേറ്റഡ് കണങ്ങളെ ഉണക്കിയതിനു ശേഷവും ടാബ്ലെറ്റിംഗിന് മുമ്പും അളക്കുന്നു.
മറ്റ് മില്ലിംഗ് സാങ്കേതികവിദ്യകളുമായി താരതമ്യപ്പെടുത്തുമ്പോൾ, കോൺ മിൽ ഫാർമസ്യൂട്ടിക്കൽ നിർമ്മാതാക്കൾക്ക് മറ്റ് പ്രത്യേക നേട്ടങ്ങളും വാഗ്ദാനം ചെയ്യുന്നു. കുറഞ്ഞ ശബ്ദം, കൂടുതൽ യൂണിഫോം കണികാ വലിപ്പം, ഡിസൈൻ ഫ്ലെക്സിബിലിറ്റി, ഉയർന്ന ശേഷി എന്നിവ ഈ നേട്ടങ്ങളിൽ ഉൾപ്പെടുന്നു.
ഇന്ന് വിപണിയിലെ ഏറ്റവും നൂതനമായ മില്ലിംഗ് സാങ്കേതികവിദ്യ മികച്ച ത്രൂപുട്ടും ഉൽപ്പന്ന വലുപ്പ വിതരണവും വാഗ്ദാനം ചെയ്യുന്നു. കൂടാതെ, അവ വേരിയബിൾ സീവ് (സ്ക്രീൻ), ഇംപെല്ലർ ഓപ്ഷനുകൾ എന്നിവയിൽ ലഭ്യമാണ്. കുറഞ്ഞ സാന്ദ്രതയുള്ള വസ്തുക്കൾ ഉപയോഗിക്കുമ്പോൾ, നേരായ ബാറുകൾ ഉപയോഗിച്ച് രൂപകൽപ്പന ചെയ്ത മില്ലുകളെ അപേക്ഷിച്ച് ഒരു അരിപ്പയ്ക്ക് 50 ശതമാനത്തിലധികം ത്രൂപുട്ട് വർദ്ധിപ്പിക്കാൻ കഴിയും. ചില സന്ദർഭങ്ങളിൽ, ഉപയോക്താക്കൾ മണിക്കൂറിൽ 3 ടൺ വരെ യൂണിറ്റ് ഉൽപ്പാദന ശേഷി നേടിയിട്ടുണ്ട്.
പൊടി രഹിത കോൺ മില്ലിങ് കൈവരിക്കുന്നു
മില്ലിംഗ് പൊടി സൃഷ്ടിക്കുന്നുവെന്ന് എല്ലാവർക്കും അറിയാം, ഇത് പൊടി അടങ്ങിയിട്ടില്ലെങ്കിൽ ഓപ്പറേറ്റർമാർക്കും ഫാർമസ്യൂട്ടിക്കൽ പ്രോസസ്സിംഗ് പരിതസ്ഥിതിക്കും പ്രത്യേകിച്ച് അപകടകരമാണ്. പൊടി തടയാൻ നിരവധി മാർഗങ്ങളുണ്ട്.
കോൺ മിൽ വഴി ചേരുവകൾ നൽകുന്നതിന് ഗുരുത്വാകർഷണത്തെ ആശ്രയിക്കുന്ന പൂർണ്ണമായും ഇൻ-ലൈൻ പ്രക്രിയയാണ് ബിൻ-ടു-ബിൻ മില്ലിങ്. സാങ്കേതിക വിദഗ്ധർ മില്ലിന് താഴെ ഒരു ബിൻ സ്ഥാപിക്കുന്നു, കൂടാതെ മില്ലിന് മുകളിൽ സ്ഥാപിച്ചിരിക്കുന്ന ഒരു ബിൻ മില്ലിലേക്ക് മെറ്റീരിയലുകൾ പുറത്തുവിടുന്നു. ഗ്രാവിറ്റി മെറ്റീരിയൽ മില്ലിംഗ് ശേഷം താഴെ കണ്ടെയ്നർ നേരിട്ട് കടന്നു അനുവദിക്കുന്നു. ഇത് ഉൽപ്പന്നത്തെ തുടക്കം മുതൽ ഒടുക്കം വരെ നിലനിർത്തുന്നു, അതുപോലെ തന്നെ മെറ്റീരിയൽ കൈമാറ്റം ചെയ്യുന്നത് എളുപ്പമാക്കുന്നു.
മറ്റൊരു രീതി വാക്വം ട്രാൻസ്ഫർ ആണ്, ഇത് ഒരു ഇൻ-ലൈൻ പ്രക്രിയ കൂടിയാണ്. ഈ പ്രക്രിയയിൽ പൊടി അടങ്ങിയിരിക്കുന്നു, കൂടാതെ ഉപഭോക്താക്കൾക്ക് ഉയർന്ന കാര്യക്ഷമതയും ചെലവ് ലാഭവും നേടാൻ സഹായിക്കുന്നതിന് പ്രക്രിയ ഓട്ടോമേറ്റ് ചെയ്യുന്നു. ഒരു ഇൻ-ലൈൻ വാക്വം ട്രാൻസ്ഫർ സിസ്റ്റം ഉപയോഗിച്ച്, ടെക്നീഷ്യൻമാർക്ക് കോണിൻ്റെ ച്യൂട്ടിലൂടെ മെറ്റീരിയലുകൾ നൽകാനും അവയെ മിൽ ഔട്ട്ലെറ്റിൽ നിന്ന് സ്വയമേവ വലിച്ചെടുക്കാനും കഴിയും. അങ്ങനെ, തുടക്കം മുതൽ അവസാനം വരെ, പ്രക്രിയ പൂർണ്ണമായും അടച്ചിരിക്കുന്നു.
അവസാനമായി, മില്ലിംഗ് സമയത്ത് നല്ല പൊടികൾ അടങ്ങിയിരിക്കാൻ ഐസൊലേറ്റർ മില്ലിംഗ് ശുപാർശ ചെയ്യുന്നു. ഈ രീതി ഉപയോഗിച്ച്, കോൺ മിൽ ഒരു മതിൽ ഫിക്സിംഗ് ഫ്ലേഞ്ചിലൂടെ ഒരു ഐസൊലേറ്ററുമായി സംയോജിപ്പിക്കുന്നു. കോൺ മില്ലിൻ്റെ ഫ്ലേഞ്ചും കോൺഫിഗറേഷനും കോൺ മിൽ തലയുടെ ഫിസിക്കൽ ഡിവിഷൻ ഐസൊലേറ്ററിന് പുറത്തുള്ള പ്രോസസ്സിംഗ് ഏരിയ വഴി അനുവദിക്കുന്നു. ഈ കോൺഫിഗറേഷൻ ഐസൊലേറ്ററിനുള്ളിൽ ഗ്ലൗ ബോക്സ് വഴി ഏതെങ്കിലും ക്ലീനിംഗ് നടത്താൻ അനുവദിക്കുന്നു. ഇത് പൊടി എക്സ്പോഷർ സാധ്യത കുറയ്ക്കുകയും പ്രോസസ്സിംഗ് ലൈനിൻ്റെ മറ്റ് ഭാഗങ്ങളിലേക്ക് പൊടി കൈമാറ്റം ചെയ്യുന്നത് തടയുകയും ചെയ്യുന്നു.
ചുറ്റിക മില്ലിങ്
ചില ഫാർമസ്യൂട്ടിക്കൽ പ്രോസസ്സിംഗ് നിർമ്മാതാക്കൾ ടർബോ മില്ലുകൾ എന്നും വിളിക്കുന്ന ചുറ്റിക മില്ലുകൾ സാധാരണയായി ഗവേഷണത്തിനും ഉൽപ്പന്ന വികസനത്തിനും തുടർച്ചയായ അല്ലെങ്കിൽ ബാച്ച് ഉൽപ്പാദനത്തിനും അനുയോജ്യമാണ്. മയക്കുമരുന്ന് ഡെവലപ്പർമാർക്ക് മിൽ ചെയ്യാൻ ബുദ്ധിമുട്ടുള്ള എപിഐകളുടെയും മറ്റ് പദാർത്ഥങ്ങളുടെയും കൃത്യമായ കണിക കുറയ്ക്കൽ ആവശ്യമായി വരുന്ന സന്ദർഭങ്ങളിൽ അവർ പലപ്പോഴും ഉപയോഗിക്കപ്പെടുന്നു. കൂടാതെ, ഹാമർ മില്ലുകൾ ഉപയോഗിച്ച് തകർന്ന ടാബ്ലറ്റുകൾ പരിഷ്കരിക്കുന്നതിനായി പൊടിച്ച് പൊടിച്ച് വീണ്ടെടുക്കാൻ കഴിയും.
ഉദാഹരണത്തിന്, പരിശോധനയിൽ, ചില നിർമ്മിത ടാബ്ലെറ്റുകൾ വിവിധ കാരണങ്ങളാൽ ഉപഭോക്താവിൻ്റെ മാനദണ്ഡങ്ങൾക്കനുസൃതമായിരിക്കില്ല: തെറ്റായ കാഠിന്യം, മോശം രൂപം, അമിതഭാരം അല്ലെങ്കിൽ ഭാരക്കുറവ്. അത്തരം സന്ദർഭങ്ങളിൽ, നിർമ്മാതാവിന് മെറ്റീരിയലുകൾക്ക് നഷ്ടം വരുത്തുന്നതിനുപകരം ടാബ്ലെറ്റുകൾ പൊടിച്ച രൂപത്തിലേക്ക് തിരികെ കൊണ്ടുവരാൻ തിരഞ്ഞെടുക്കാം. ടാബ്ലെറ്റുകൾ വീണ്ടും മില്ലിംഗ് ചെയ്യുകയും ഉൽപാദനത്തിലേക്ക് തിരികെ കൊണ്ടുവരുകയും ചെയ്യുന്നത് ആത്യന്തികമായി മാലിന്യങ്ങൾ കുറയ്ക്കുകയും ഉൽപാദനക്ഷമത വർദ്ധിപ്പിക്കുകയും ചെയ്യുന്നു. ടാബ്ലെറ്റുകളുടെ ഒരു ബാച്ച് സ്പെസിഫിക്കേഷനുകൾ പാലിക്കാത്ത മിക്കവാറും എല്ലാ സാഹചര്യങ്ങളിലും, നിർമ്മാതാക്കൾക്ക് പ്രശ്നം മറികടക്കാൻ ഒരു ചുറ്റിക മിൽ ഉപയോഗിക്കാം.
മണിക്കൂറിൽ 1,500 കിലോഗ്രാം വരെ ഉൽപ്പാദിപ്പിക്കുമ്പോൾ 1,000 ആർപിഎം മുതൽ 6,000 ആർപിഎം വരെ വേഗതയിൽ പ്രവർത്തിക്കാൻ ഹാമർ മില്ലുകൾക്ക് കഴിയും. ഇത് നേടുന്നതിന്, ചില മില്ലുകൾ ഒരു ഓട്ടോമാറ്റിക് റൊട്ടേറ്റിംഗ് വാൽവ് കൊണ്ട് സജ്ജീകരിച്ചിരിക്കുന്നു, അത് സാങ്കേതിക വിദഗ്ധരെ മില്ലിംഗ് ചേമ്പർ ഓവർഫിൽ ചെയ്യാതെ ചേരുവകളാൽ തുല്യമായി നിറയ്ക്കാൻ അനുവദിക്കുന്നു. ഓവർഫിൽ തടയുന്നതിനു പുറമേ, അത്തരം ഓട്ടോമാറ്റിക് ഫീഡിംഗ് ഉപകരണങ്ങൾക്ക് മില്ലിംഗ് ചേമ്പറിലേക്കുള്ള പൊടിയുടെ ഒഴുക്ക് നിയന്ത്രിക്കാനും പ്രോസസ്സ് ആവർത്തനക്ഷമത വർദ്ധിപ്പിക്കാനും ചൂട് ഉൽപാദനം കുറയ്ക്കാനും കഴിയും.
കൂടുതൽ നൂതനമായ ചില ചുറ്റിക മില്ലുകൾക്ക് ഇരട്ട-വശങ്ങളുള്ള ബ്ലേഡ് അസംബ്ലി ഉണ്ട്, ഇത് നനഞ്ഞതോ ഉണങ്ങിയതോ ആയ ചേരുവകളുടെ പ്രവർത്തനക്ഷമത വർദ്ധിപ്പിക്കുന്നു. ബ്ലേഡിൻ്റെ ഒരു വശം ഉണങ്ങിയ വസ്തുക്കളെ തകർക്കാൻ ഒരു ചുറ്റികയായി പ്രവർത്തിക്കുന്നു, അതേസമയം കത്തി പോലുള്ള ഒരു വശം നനഞ്ഞ ചേരുവകളിലൂടെ മുറിക്കാൻ കഴിയും. ഉപയോക്താക്കൾ അവർ മില്ലിംഗ് ചെയ്യുന്ന ചേരുവകളെ അടിസ്ഥാനമാക്കി റോട്ടർ ഫ്ലിപ്പുചെയ്യുന്നു. കൂടാതെ, ചില മിൽ റോട്ടർ അസംബ്ലികൾ നിർദിഷ്ട ഉൽപ്പന്ന സ്വഭാവം ക്രമീകരിക്കുന്നതിന് വിപരീതമാക്കാവുന്നതാണ്, അതേസമയം മില്ലിൻ്റെ ഭ്രമണം മാറ്റമില്ലാതെ തുടരുന്നു.
ചില ചുറ്റിക മില്ലുകൾക്ക്, മില്ലിനായി തിരഞ്ഞെടുത്ത സ്ക്രീൻ വലുപ്പത്തെ അടിസ്ഥാനമാക്കിയാണ് കണികാ വലുപ്പം നിർണ്ണയിക്കുന്നത്. ആധുനിക ചുറ്റിക മില്ലുകൾക്ക് മെറ്റീരിയൽ വലുപ്പം 0.2 മില്ലിമീറ്റർ മുതൽ 3 മില്ലിമീറ്റർ വരെ കുറയ്ക്കാൻ കഴിയും. പ്രോസസ്സിംഗ് പൂർത്തിയായിക്കഴിഞ്ഞാൽ, മിൽ സ്ക്രീനിലൂടെ കണങ്ങളെ തള്ളുന്നു, ഇത് ഉൽപ്പന്ന വലുപ്പത്തെ നിയന്ത്രിക്കുന്നു. അന്തിമ ഉൽപ്പന്ന വലുപ്പം നിർണ്ണയിക്കാൻ ബ്ലേഡും സ്ക്രീനും സംയോജിച്ച് പ്രവർത്തിക്കുന്നു.
പോസ്റ്റ് സമയം: ഓഗസ്റ്റ്-08-2022